事例
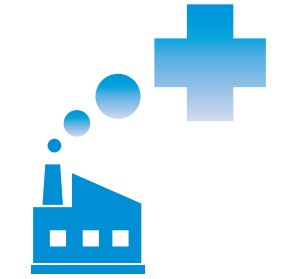
これまで実施してきた生産の安定化、設備保全の導入・改良、保全業務の整理、
地球環境負荷の低減、教育事業、保全システム、IT・DX化支援の事例を紹介します。
生産の安定化①
コンベア設備の安定化を実現
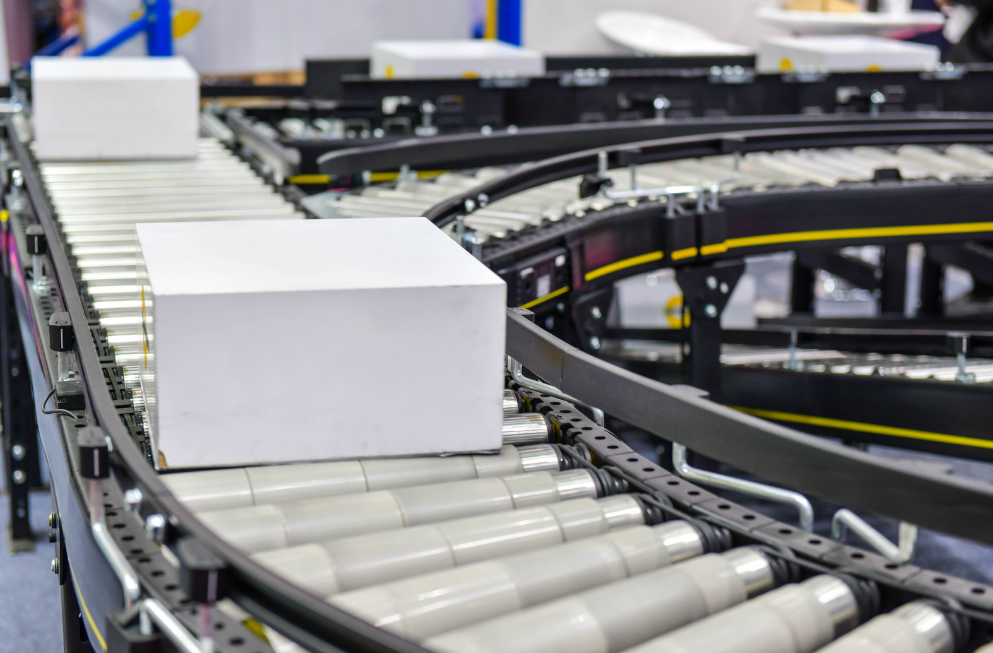
- 製品出荷事業所
- マテハン
- 日勤工場
- 工数:2年
- 稼働年数:40年
before
- 搬送設備は、全て事後対応となっており、 トラブルによるラインの停止が頻発していた
- 設備のリスト化や重要設備の把握ができ ておらず、保全計画を立てることが困難で あった
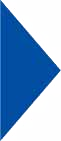
after
- 設備ごとの日常保全を計画し、実行方法を標準化して遂行した
- 工程の停止いたる重大なトラブルは4割削減され、突発故障も3割ほど削減された
- 設備全体が把握できることで、運転や工事の際の安全対策の精度が高まり、より安全・安心な現場になった
生産の安定化②
重大トラブルのゼロ化を実現
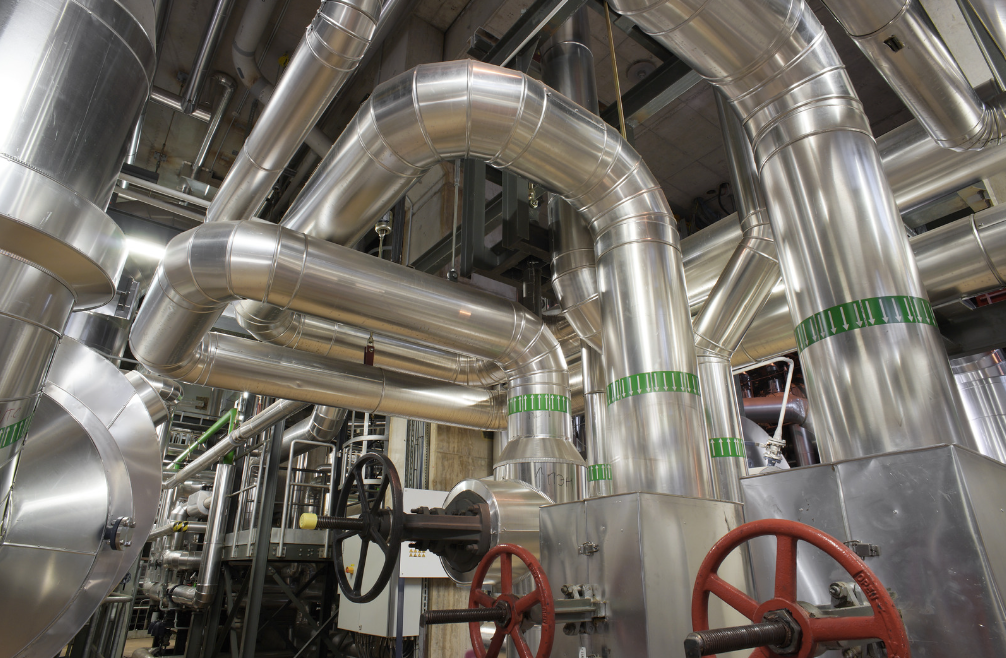
- 化学工場
- 配管類
- 24時間稼働工場
- 工数:2年
- 稼働年数:40年
before
- 熱媒ラインの管理方法がわからず、トラブルや保全費用の増加に悩んでいた
- 熱媒ラインのトラブルは、生産への影響が大きいため、早急な解決が求められた
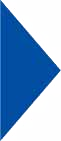
after
- 全ライン配管ルートを作成し、リスクベースでの検査計画を立てて、実行した
- 重大トラブルのゼロ化に成功、生産機会の増加に繋がった
- 保全費用の安定に貢献し、経営負荷を削減
- 重大トラブルがなくなり安心でき、生産量も増えて、 自慢できる管理方法になった
保全計画の導入・改良①
新設工場の保全計画の立案
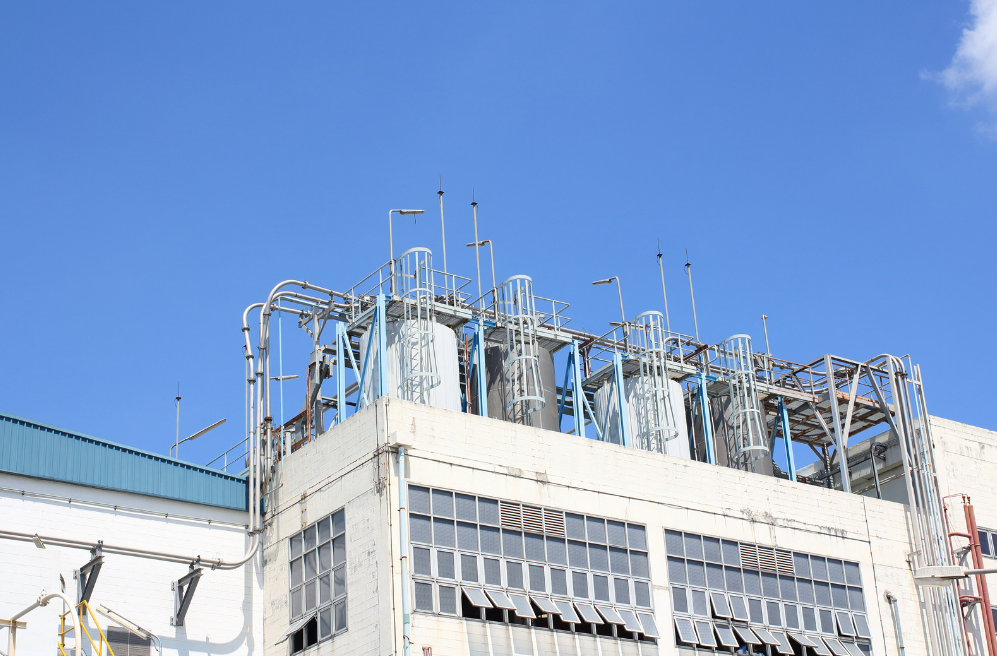
-
プラスチック製品
製造業 - 押出・造粒工程
- 日勤工場
- 工数:1年
- 稼働年数:1年
before
- 工場の安定と保全予算計画の策定が求められた
- 工程の停止時間やトラブル件数のベンチマーク設計が必要であった
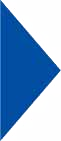
after
- 中長期の保全計画を作り、実行することで、工場を安定させた
- 保全予算や設備稼働時間のベンチマークを作成することで、経営戦略の管理指標を明確化できた
- 現場作業が楽になり、オペレーターのやる気の向上につながった。また離職率を下げる効果もあった
保全計画の導入・改良②
重要機器の保全計画の立案
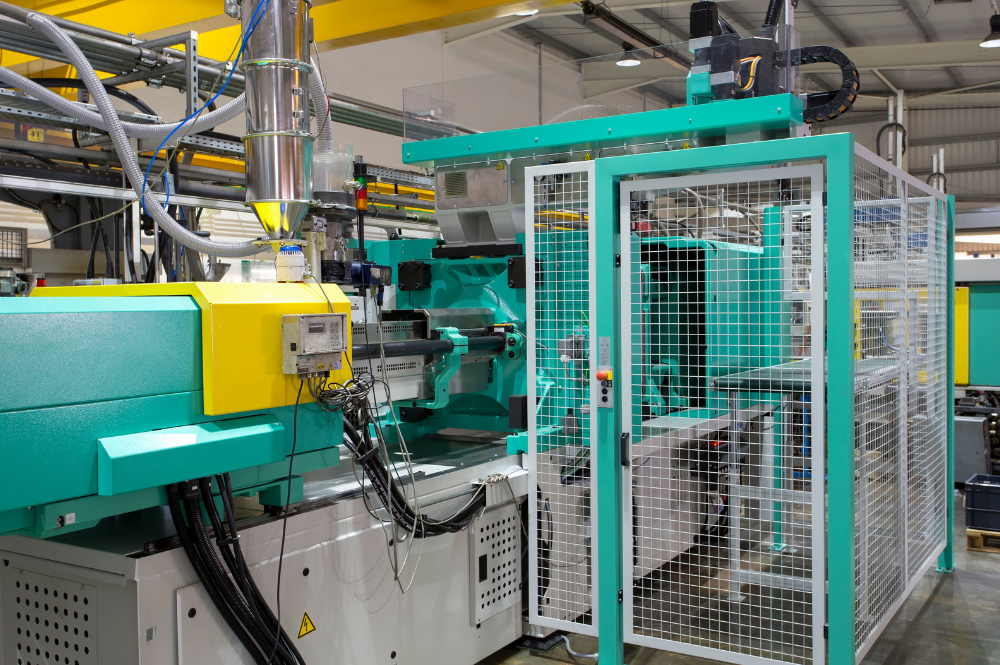
- 合成樹脂製造業
- 押出機
- 24時間稼働工場
- 工数:1年
- 稼働年数:30年
before
- 押出機の不安定が問題が、生産量低下の原因になっていた
- 現場での大きな不安材料となっていた
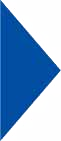
after
- 過去のトラブル対策だけでなく、未知のトラブルへ対応した保全計画の立案を行った
- トラブルリスクを軽減した
- 技術の向上や技術伝承につながった
- 万が一の際も、トラブルに早急に対応できる体制を整えたため、安心感が高まった
保全計画の導入・改良③
メンテナンス方法の再構築
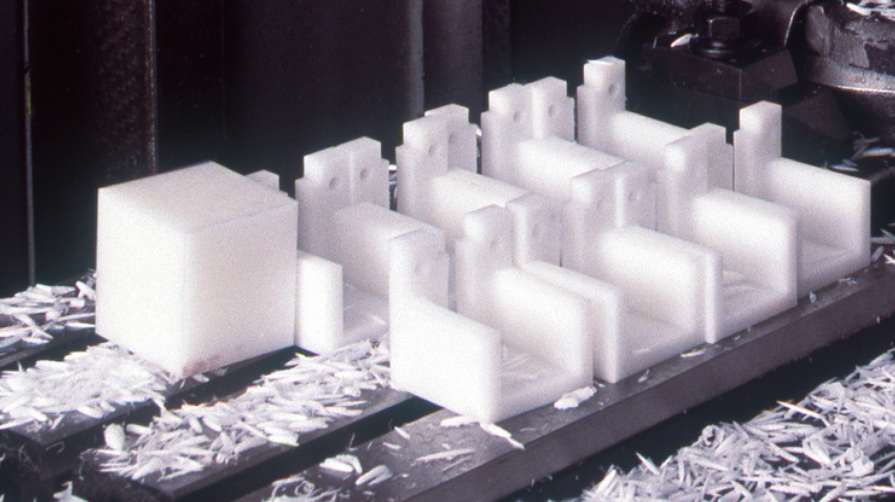
- 樹脂成型工場
- 成形機
- 24時間稼働工場
- 工数:1年
- 稼働年数:30年
before
- 油圧式の成型機で、原因不明の繰り返しトラブルが発生していた
- 生産機会の減少や、品質不良の要因になり、苦しんでいた
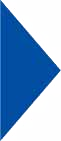
after
- 設備に気づけていない変化や不具合があると推測し、ゼロベースでメンテナンス方法を再構築した。
- 工程停止や品質トラブルにつながる重大故障のゼロ化に成功、油圧式成型機の保全費用も5割削減された
- 工程が安定し、安心して運転業務に専念できるようになった
保全業務の整理
保全業務の状況整理、フローの可視化
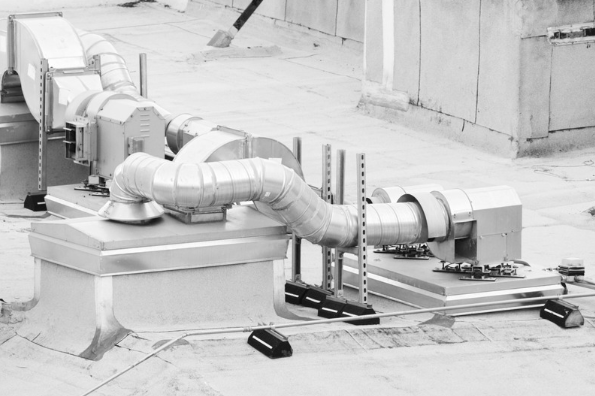
- 設備工事会社
- -
- -
- 工数:6ヶ月
- -
before
- 設備工事会社の新規事業として、保全システムのサービスを開始する
- そのサービス開始前に、工場の保全の実態や保全業務ノウハウ、保全業務フローの調査が必要となった
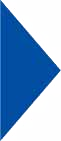
after
- 保全サービスのリリースにあたり、必要となる保全の実態及び状況を整理し、可視化した
- 一般的な工場の保全実態、保全業務ノウハウ、業務フローを可視化した
地球環境負荷の低減
排ガスの削減、省エネ化を実現
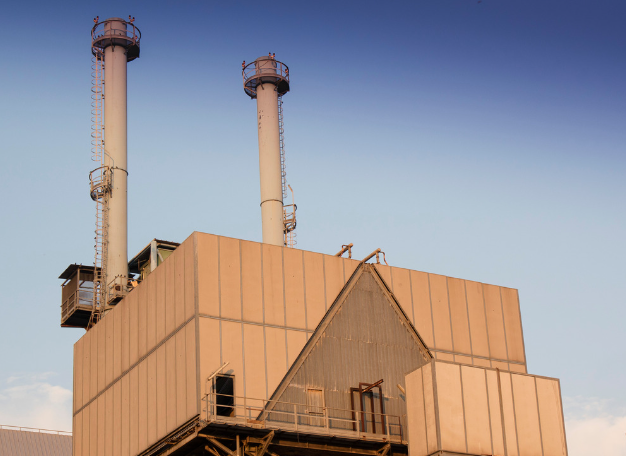
- 合成樹脂製造業
- 焼却炉
- 24時間稼働工場
- 工数:1年
- 稼働年数:10年
before
- バーナーのトラブルがあり、原因調査を行った結果、今まで気づけていなかった「燃料ガスを削減するポテンシャル」を発見した
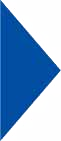
after
- 焼却炉の運転方法変更、設備改良工事を行った
- バーナートラブルの原因特定及び対策によるトラブルのゼロ化を達成した
- 燃焼ガス起因のCO2及びバーナーに使用しているガスを50%削減した
教育事業①
工事会社の若手社員教育
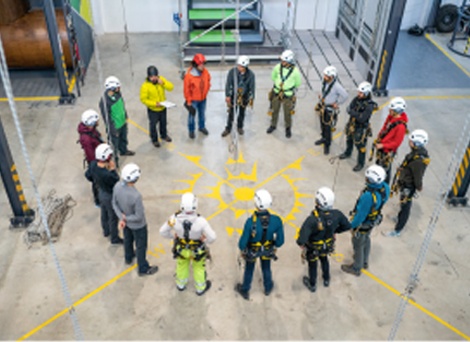
- 工事会社
- -
- -
- 工数:3ヶ月
- -
before
- 教育は、現場でのOJTがメインとなっており、集合教育ができておらず、若手社員の専門知識にバラツキがあった
- 社内で、機械設備の取り扱い教育を行う人材がおらず、社内教育の実施が難しかった
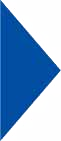
after
- 教育の内容の設計、テキストの選定~教育の実施まで行った
- 現場だけでは教育できない設備設計や設備構造の理解が社員内で広まった
- 新たな知見が得られ、社内教育の満足感が得られた
教育事業②
大学講義でのワークショップ
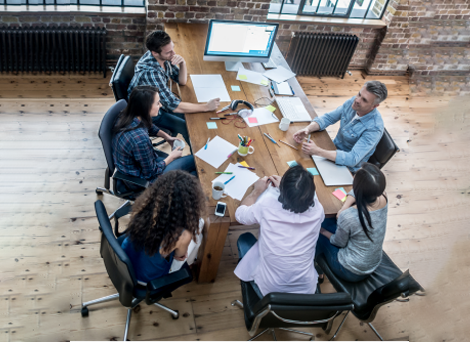
- 大学
- -
- -
- 工数:1ヶ月
- -
実施内容
- 課題解決の実践科目として、現状の企業課題課題の解決に向けたケーススタディーを講義及び発表会を実施
- 実際の企業課題のケースステディーであり、受講者はモチベーションを高く、課題に取り組むことができた
保全システム、IT・DX化支援
各種設備工事の検討支援
各種改善
工事に対応
工場ごとにあるべき姿を共に考え抜き、経済的で効果的な機器の選定、設置を行います
回転機器への
振動センサー設置
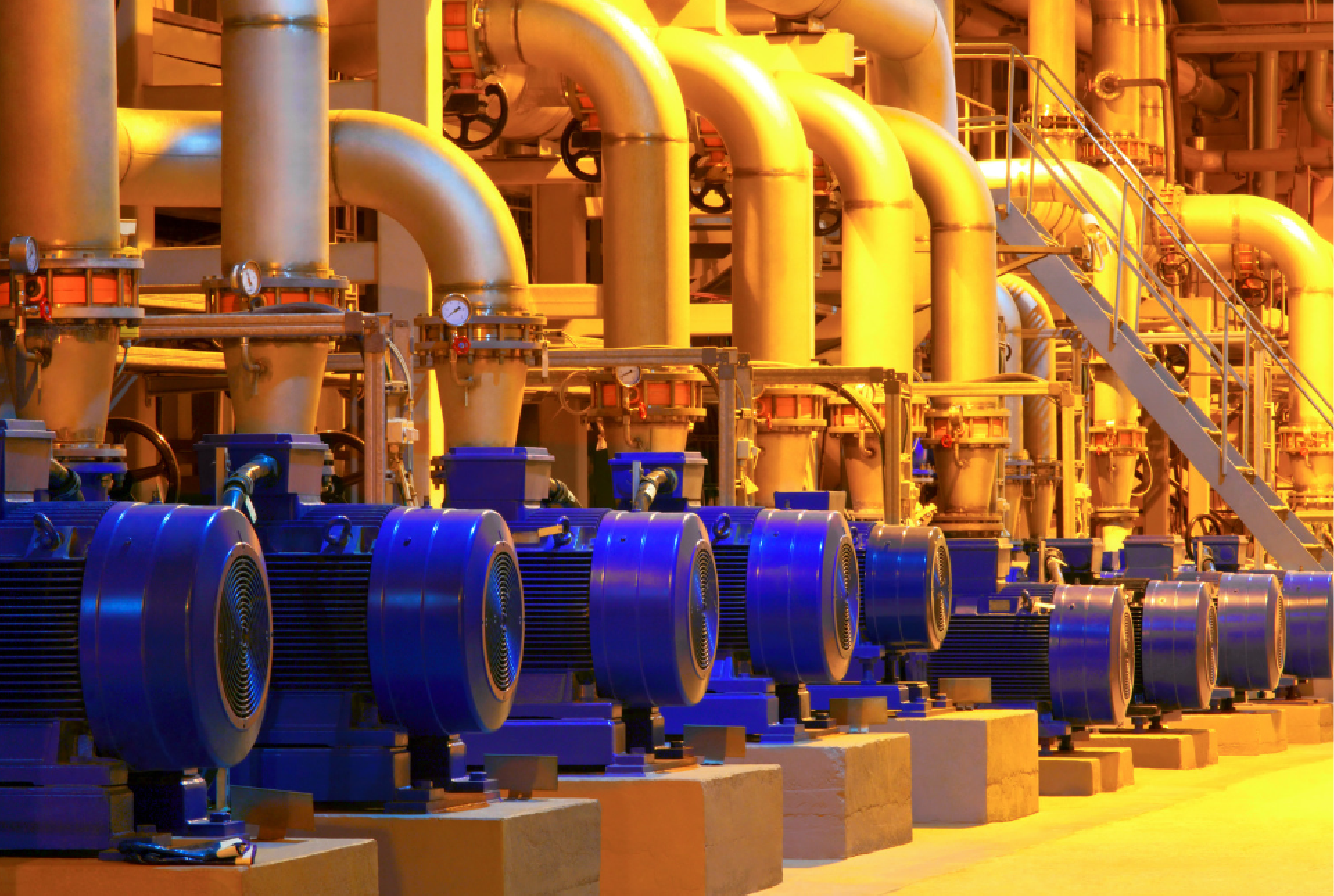
品質チェック用
カメラ設置
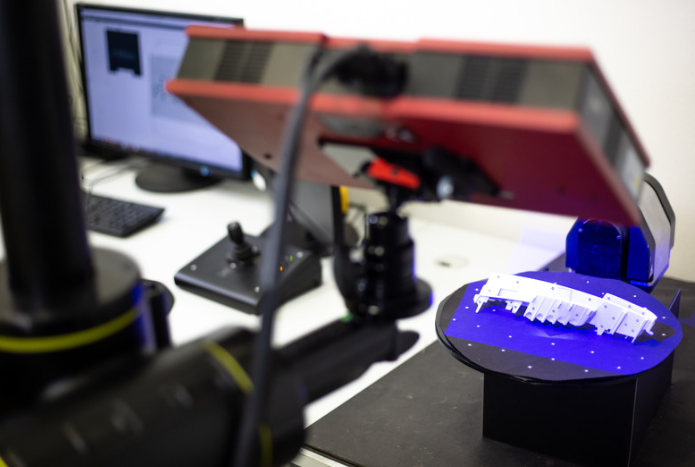
金属検知器
設置
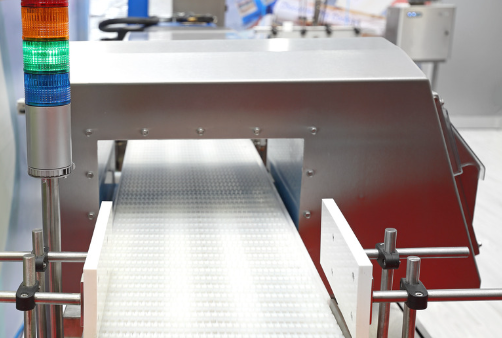